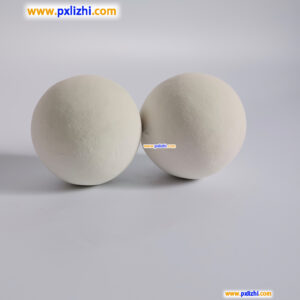
# Inert Ceramic Ball Applications and Benefits
## What Are Inert Ceramic Balls?
Inert ceramic balls are high-performance ceramic spheres designed for industrial applications where chemical inertness and thermal stability are crucial. These balls are manufactured from high-purity alumina or other ceramic materials, offering exceptional resistance to corrosion, high temperatures, and mechanical wear.
## Key Applications of Inert Ceramic Balls
### 1. Chemical Processing Industry
Inert ceramic balls serve as excellent catalyst supports and tower packing materials in chemical reactors. Their non-reactive nature prevents unwanted chemical reactions while providing optimal surface area for catalytic processes.
### 2. Petroleum Refining
These ceramic balls are widely used in oil refining processes as support media for catalysts in fixed-bed reactors. They help distribute gases and liquids evenly while withstanding harsh operating conditions.
### 3. Environmental Protection Systems
In air and water treatment systems, inert ceramic balls act as filtration media and support structures for biological treatment processes, effectively removing contaminants without degrading over time.
### 4. Thermal Insulation Applications
Keyword: inert ceramic ball
Due to their excellent thermal properties, these ceramic balls are used as insulating materials in high-temperature furnaces and kilns, helping to maintain consistent heat distribution.
## Benefits of Using Inert Ceramic Balls
### 1. Exceptional Chemical Resistance
The inert nature of these ceramic balls makes them resistant to most acids, alkalis, and organic solvents, ensuring long-term performance in corrosive environments.
### 2. High Temperature Stability
Withstanding temperatures up to 1600°C (2912°F), these balls maintain their structural integrity in extreme heat conditions where metal alternatives would fail.
### 3. Mechanical Strength
Their high compressive strength and abrasion resistance allow for extended service life even under heavy loads and turbulent flow conditions.
### 4. Cost-Effective Solution
While the initial investment might be higher than some alternatives, the longevity and reduced maintenance requirements of inert ceramic balls often result in lower total cost of ownership.
### 5. Improved Process Efficiency
The uniform size and spherical shape of these balls promote better fluid distribution and reduce pressure drops in packed bed applications, leading to more efficient operations.
## Choosing the Right Inert Ceramic Ball
When selecting inert ceramic balls for your application, consider factors such as:
- Material composition (alumina content typically ranges from 23% to 99%)
- Size specifications (common diameters range from 3mm to 50mm)
- Operating temperature range
- Chemical exposure requirements
- Mechanical load conditions
Consulting with a specialist can help ensure you select the optimal ceramic ball for your specific industrial needs, maximizing performance and cost-effectiveness.