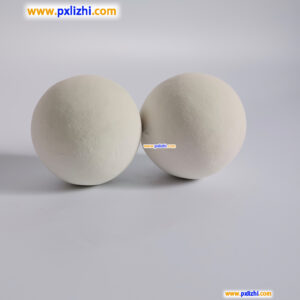
# Inert Ceramic Balls: Essential Components for Industrial Applications
## What Are Inert Ceramic Balls?
Inert ceramic balls are spherical ceramic materials designed to withstand extreme temperatures, corrosive environments, and high-pressure conditions without reacting chemically with the substances they come into contact with. These small but mighty components play a crucial role in various industrial processes where chemical inertness and thermal stability are paramount.
Manufactured from high-quality alumina or other ceramic materials, these balls typically range in size from a few millimeters to several centimeters in diameter. Their uniform shape and consistent properties make them ideal for numerous applications across different industries.
## Key Properties of Inert Ceramic Balls
The effectiveness of inert ceramic balls stems from their unique combination of physical and chemical properties:
– High temperature resistance (up to 1600°C)
– Excellent chemical inertness
– Superior mechanical strength
– Low thermal expansion coefficient
– High corrosion resistance
– Good thermal shock resistance
– Uniform size and shape distribution
These properties make them particularly valuable in processes where maintaining purity and preventing contamination are critical.
## Industrial Applications of Inert Ceramic Balls
### 1. Petrochemical Industry
In the petrochemical sector, inert ceramic balls serve as support media in reactors and towers. They help distribute gases and liquids evenly while protecting more expensive catalysts from mechanical damage. Their thermal stability makes them ideal for processes like catalytic reforming and hydroprocessing.
### 2. Chemical Processing
Chemical manufacturers use these ceramic balls as packing material in distillation columns and as catalyst supports in various synthesis processes. Their inert nature ensures they don’t interfere with chemical reactions while providing excellent heat transfer properties.
Keyword: inert ceramic ball
### 3. Environmental Protection
Inert ceramic balls find application in environmental protection systems, particularly in scrubbers and other air pollution control equipment. They help maximize surface area for gas-liquid contact in processes designed to remove pollutants from industrial emissions.
### 4. Refining Operations
Refineries utilize these ceramic components in multiple processes, including:
– Fluid catalytic cracking units
– Hydrotreating reactors
– Reforming units
– Isomerization processes
Their ability to withstand harsh conditions makes them indispensable in these applications.
## Benefits of Using Inert Ceramic Balls
The advantages of incorporating inert ceramic balls into industrial processes include:
– Extended equipment lifespan due to reduced wear and tear
– Improved process efficiency through better fluid distribution
– Lower maintenance costs
– Enhanced product purity
– Reduced energy consumption in some applications
– Long-term stability in aggressive environments
## Selection Criteria for Inert Ceramic Balls
When choosing inert ceramic balls for specific applications, several factors should be considered:
1. Chemical composition (alumina content typically ranges from 23% to 99%)
2. Size and diameter specifications
3. Crushing strength requirements
4. Operating temperature range
5. Pressure conditions
6. Chemical environment
7. Thermal shock resistance needs
Proper selection ensures optimal performance and longevity in the intended application.
## Maintenance and Handling
While inert ceramic balls are durable, proper handling and maintenance can extend their service life:
– Store in dry conditions to prevent moisture absorption
– Handle carefully to avoid chipping or cracking
– Clean periodically to remove accumulated deposits
– Inspect regularly for signs of wear or degradation
– Replace when performance begins to decline
## Future Trends in Inert Ceramic Ball Technology
The inert ceramic ball industry continues to evolve with advancements in materials science and manufacturing techniques. Emerging trends include:
– Development of ceramic compositions with even higher temperature resistance
– Improved manufacturing processes for more consistent quality
– Customized solutions for specific industrial applications
– Integration with smart monitoring systems
– Enhanced surface treatments for specialized applications
These innovations promise to expand the range of applications and improve performance in existing uses.
## Conclusion
Inert ceramic balls may be small in size, but their impact on industrial processes is substantial. From petrochemical refining to environmental protection, these versatile components provide reliable performance in some of the most