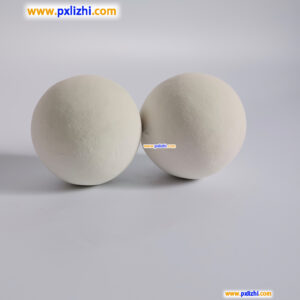
# Inert Ceramic Ball Applications in Industrial Processes
## Introduction to Inert Ceramic Balls
Inert ceramic balls are widely used in various industrial processes due to their excellent chemical stability, high temperature resistance, and mechanical strength. These small spherical ceramic materials play a crucial role in optimizing industrial operations across multiple sectors.
## Key Properties of Inert Ceramic Balls
Before exploring their applications, it’s important to understand the fundamental characteristics that make inert ceramic balls so valuable:
– High chemical inertness
– Exceptional thermal stability
– Superior mechanical strength
– Low water absorption
– Excellent corrosion resistance
– Uniform size and shape
## Major Industrial Applications
### 1. Petrochemical Industry
In the petrochemical sector, inert ceramic balls serve multiple purposes:
– As catalyst supports in reactors
– For bed support in distillation columns
– As packing material in absorption towers
– For fluid distribution in trickle-bed reactors
### 2. Chemical Processing
Chemical manufacturers utilize inert ceramic balls for:
– Protecting catalysts from contamination
– Improving gas distribution in reactors
– Preventing channeling in packed beds
Keyword: inert ceramic ball
– Acting as thermal insulators in high-temperature processes
### 3. Environmental Protection
Environmental applications include:
– Supporting media in scrubbers for gas purification
– Packing material in wastewater treatment systems
– Catalyst carriers for emission control
– Filtration media for industrial effluents
### 4. Metallurgical Industry
Metallurgical processes benefit from inert ceramic balls through:
– Heat exchange media in high-temperature furnaces
– Support materials for metal powder production
– Insulation layers in metal treatment processes
– Protective barriers in molten metal handling
## Selection Criteria for Industrial Use
When choosing inert ceramic balls for industrial applications, consider:
– Operating temperature range
– Chemical compatibility with process media
– Required mechanical strength
– Size distribution requirements
– Pressure drop considerations
– Thermal shock resistance
## Advantages Over Alternative Materials
Inert ceramic balls offer several benefits compared to other packing materials:
– Longer service life than metal or plastic alternatives
– Better resistance to harsh chemical environments
– Higher temperature tolerance
– Lower maintenance requirements
– More consistent performance over time
## Future Trends in Industrial Applications
The use of inert ceramic balls continues to evolve with:
– Development of advanced ceramic compositions
– Improved manufacturing techniques for better uniformity
– Customized solutions for specific industrial needs
– Integration with smart monitoring systems
– Expanded use in emerging green technologies
## Conclusion
Inert ceramic balls have become indispensable components in numerous industrial processes. Their unique combination of properties makes them ideal for demanding applications where reliability and performance are critical. As industries continue to push the boundaries of process efficiency and environmental responsibility, the role of inert ceramic balls is expected to grow even more significant.