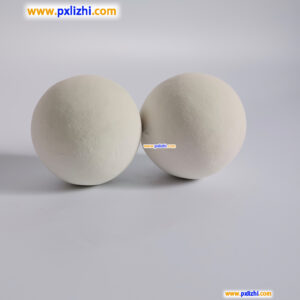
# Inert Ceramic Ball Applications in Industrial Processes
## Introduction to Inert Ceramic Balls
Inert ceramic balls are widely used in various industrial processes due to their excellent chemical stability, high mechanical strength, and thermal resistance. These small spherical ceramic materials play a crucial role in supporting catalysts, distributing gases, and protecting sensitive equipment in harsh industrial environments.
## Key Properties of Inert Ceramic Balls
The effectiveness of inert ceramic balls in industrial applications stems from their unique properties:
– High temperature resistance (up to 1600°C)
– Excellent chemical inertness
– Superior mechanical strength
– Low water absorption
– Good thermal shock resistance
– Uniform size distribution
## Major Industrial Applications
### 1. Petrochemical Industry
Inert ceramic balls serve as catalyst supports and bed separators in petrochemical reactors. They help distribute gases evenly and prevent catalyst particles from clogging the reactor. Common applications include:
– Hydroprocessing units
– Reforming processes
– Ethylene production
– Aromatics production
### 2. Environmental Protection
These ceramic balls are extensively used in environmental protection applications:
Keyword: inert ceramic ball
– Flue gas treatment systems
– Waste gas purification towers
– Desulfurization equipment
– VOC treatment systems
### 3. Chemical Industry
In chemical manufacturing, inert ceramic balls provide:
– Support for catalysts in ammonia synthesis
– Protection for sensitive equipment in sulfuric acid production
– Media for heat exchange in exothermic reactions
– Distribution of reactants in fluidized beds
### 4. Refining Processes
Oil refineries utilize inert ceramic balls in:
– Hydrotreating units
– Catalytic reforming
– Isomerization processes
– Alkylation units
## Selection Criteria for Industrial Applications
When choosing inert ceramic balls for specific industrial processes, engineers consider several factors:
– Operating temperature range
– Chemical compatibility with process media
– Required mechanical strength
– Size and surface area requirements
– Pressure drop considerations
– Thermal shock resistance needs
## Advantages Over Alternative Materials
Inert ceramic balls offer distinct advantages compared to metal or plastic alternatives:
– Longer service life in corrosive environments
– Better performance at high temperatures
– Lower maintenance requirements
– More consistent performance over time
– Reduced contamination risk
## Future Trends in Industrial Applications
The use of inert ceramic balls continues to evolve with technological advancements:
– Development of specialized formulations for extreme conditions
– Integration with advanced catalyst systems
– Application in emerging green technologies
– Use in novel reactor designs
– Implementation in carbon capture systems
As industrial processes become more demanding, inert ceramic balls will remain essential components in ensuring efficient, reliable, and safe operations across multiple sectors.